Experts in cold forging since 1981
We began building our experience in the 1980s, first in the production of spark plugs and other metal components, then increasingly developing our knowledge in cold forging. Over time, we have deepened our experience in the cold forging process to specialize in the production of complex components.
In 2015 the company underwent a further revolution and FCF Fontanafredda Cold Forging was inaugurated: even without the original founders, the company is still growing today on solid foundations of high know-how and specialist experience in the cold forging of all employees.
Today we are a close-knit, equal and dynamic team, driven by values such as workplace safety, sustainability and the enhancement of all the people who work every day for the continuous growth and innovation of our company.
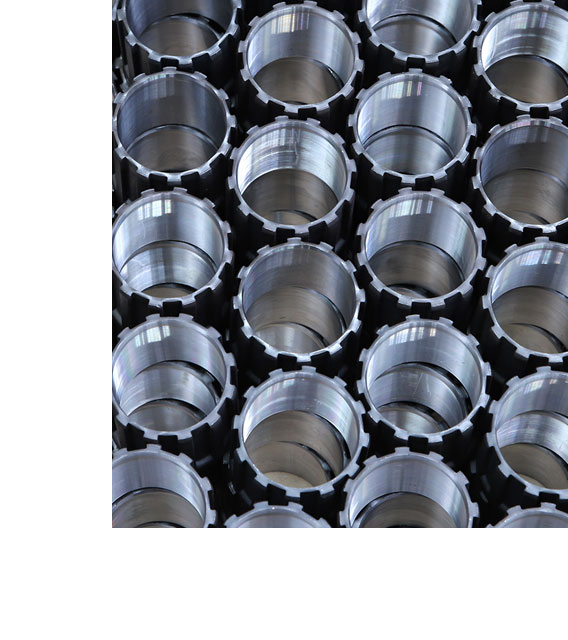
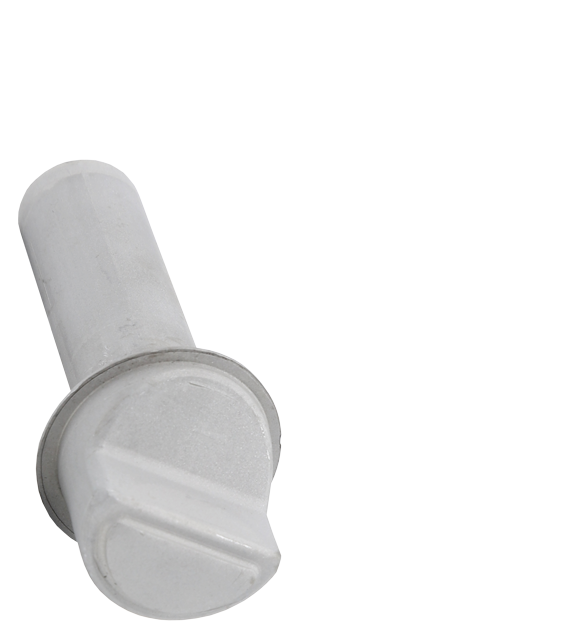
Specialized Collaborators
Pieces produced per year
of Plant
turnover
of exports to Europe
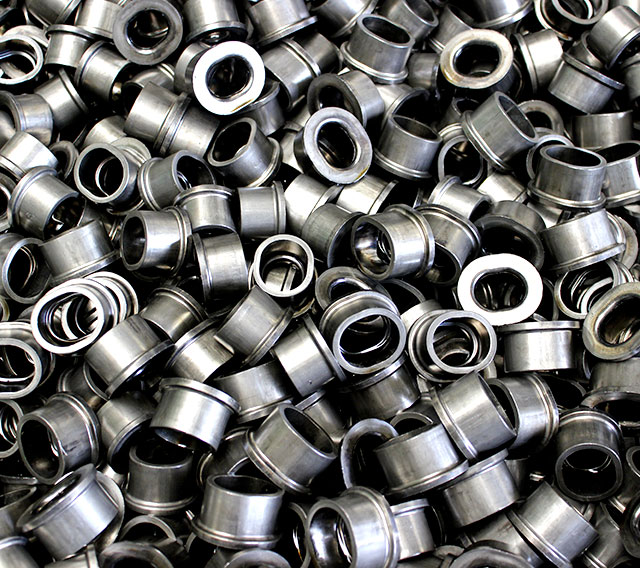
Production of metal components
Four partners found the company, originally dedicated to the production of metal components, such as spark plugs.
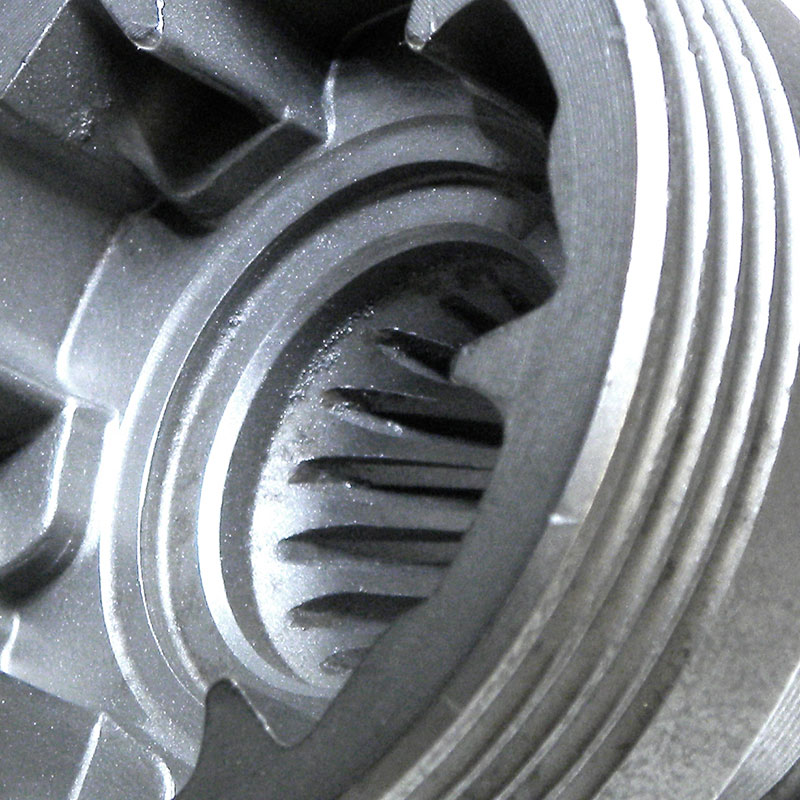
We develop expertise in cold forging
To distinguish itself from the strong competition, the company further develops its knowledge in the field of cold forging.
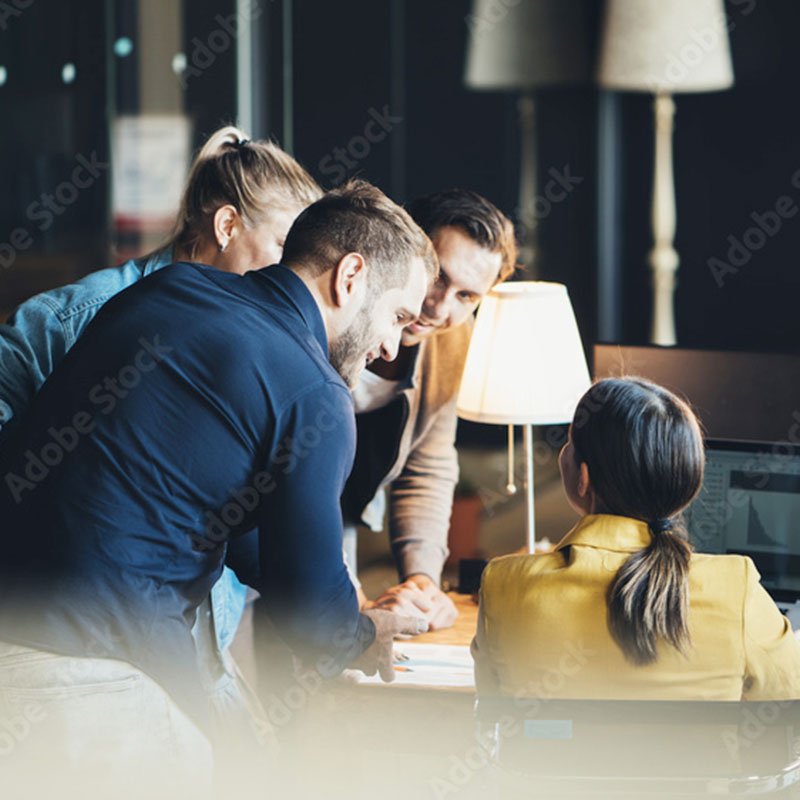
An international collaboration
The company becomes part of a French industrial group.
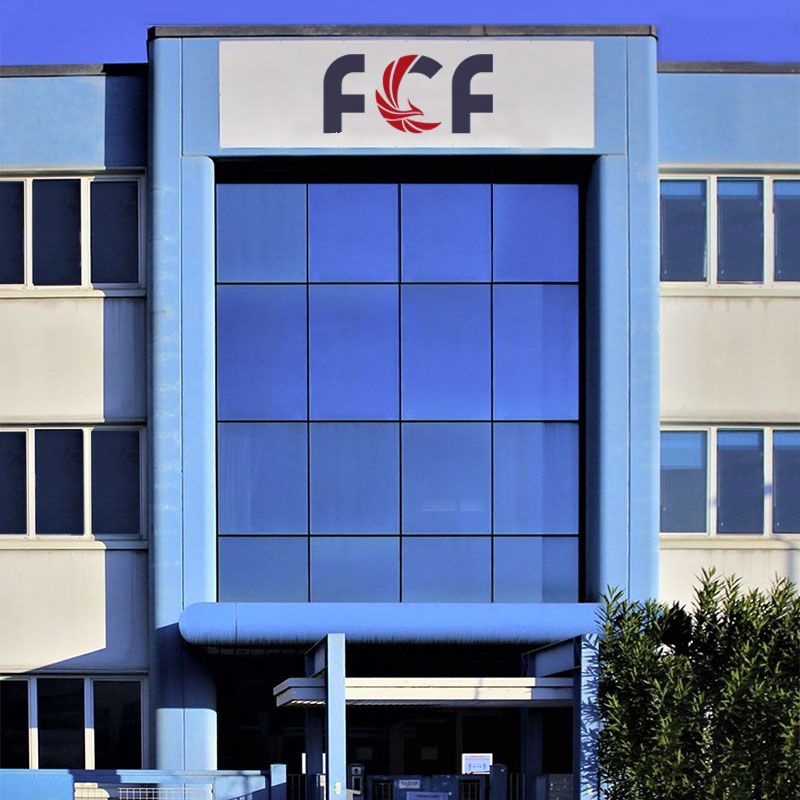
Independent company FCF was born
The company leaves the group and becomes the independent company FCF Fontanafredda Cold Forging
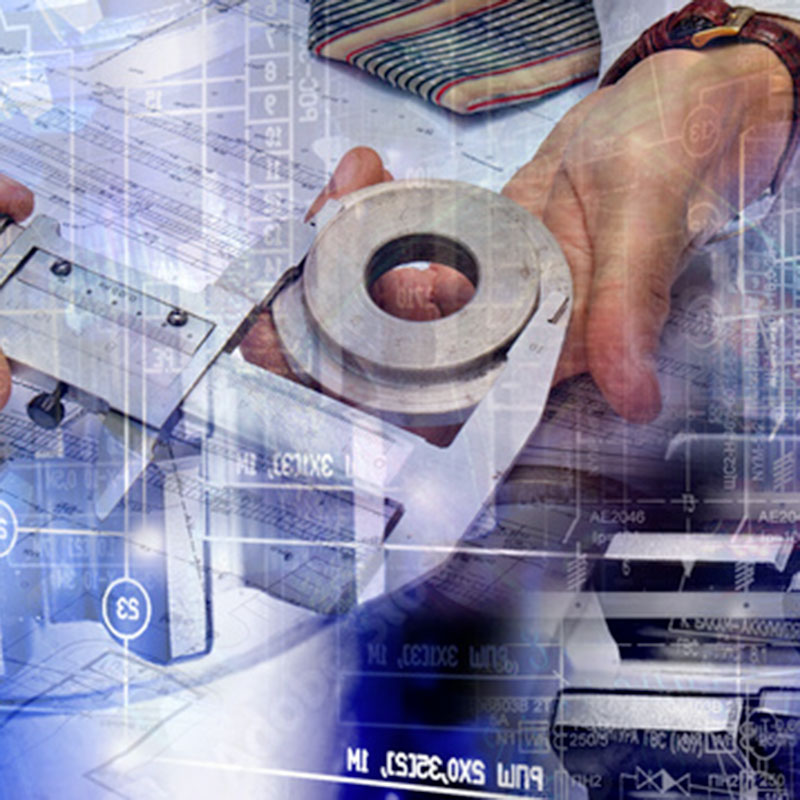
The evolution towards electric
The company anticipates the ecological transition in the automotive sector by starting to convert its production to steering and brake components suitable for any type of engine including electric
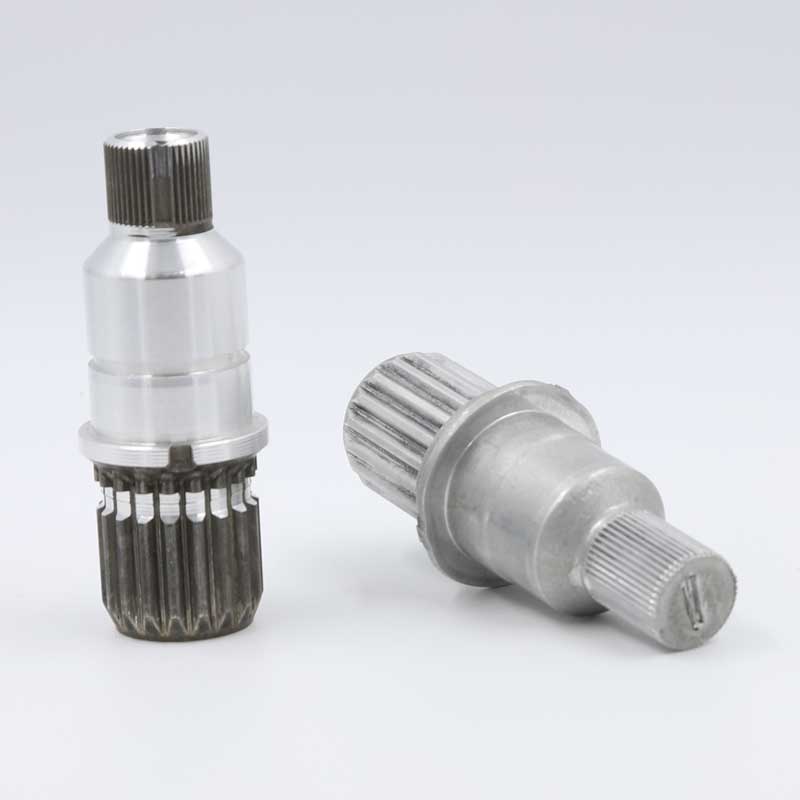
From steel to aluminium
We use our knowledge in aluminum forging for the production of lighter and more performing components
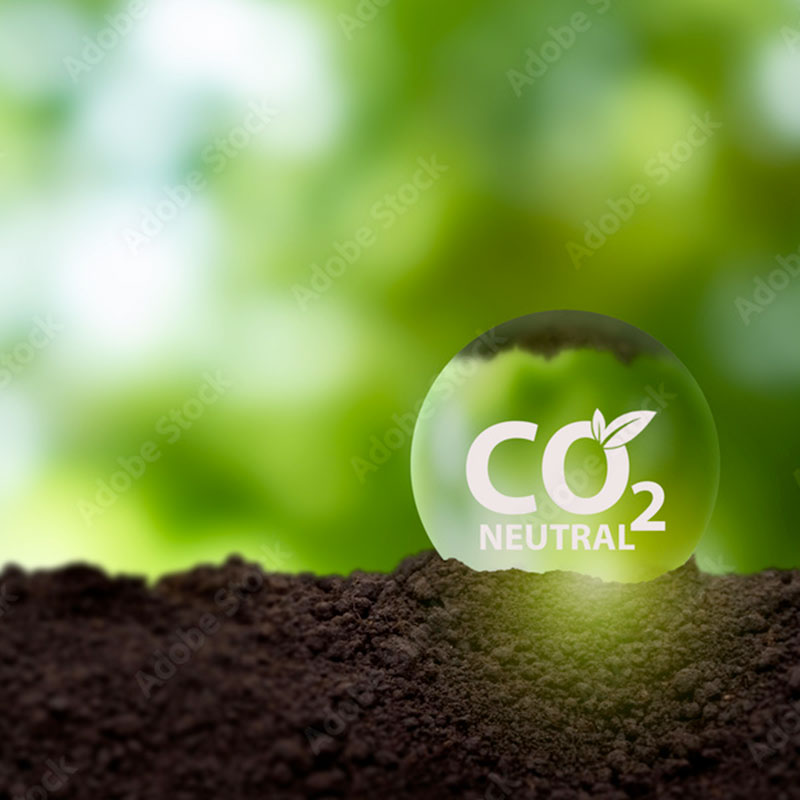
Sustainability and innovation
We aim to make our company more and more environmentally sustainable by innovating and improving our processes every day.
TECHNOLOGY
EXPERIENCE
INNOVATION
SUSTAINABILITY
Less waste and more savings with cold forging
We produce Advanced Form Part with cold forming technology, with less waste of material and greater cost and time savings compared to machining process from bar.
Specialists in cold forging since 1981
We started in the 80s with the production of fastening systems and hydraulic fittings. Over the years, we then refined our experience in cold forging, specializing in the production of highly complex parts, especially for the European automotive industry.
Creativity and experience to give form to your ideas
We carry out the entire process of study, design and development of the molds internally, working in co-design with the Customer from the early stages. We use two simulation software to verify the feasibility of the product and related equipment with the aim of optimizing its configuration.
Our goals for sustainable development
We put workplace safety and respect for the environment first. Thanks to the intrinsic characteristics of cold forming, with our daily actions and our adherence to the 2030 Agenda, we comply with environmental regulations and reduce our environmental impact as much as possible.
Highly complex components for automotive and industry
Given the great commitment required by this technology for the design and construction of moulds, we have always turned mainly to the automotive sector.
Now, thanks also to the additional skills acquired in the field of turning, we bring our know-how in the production of complex components to other sectors as well.
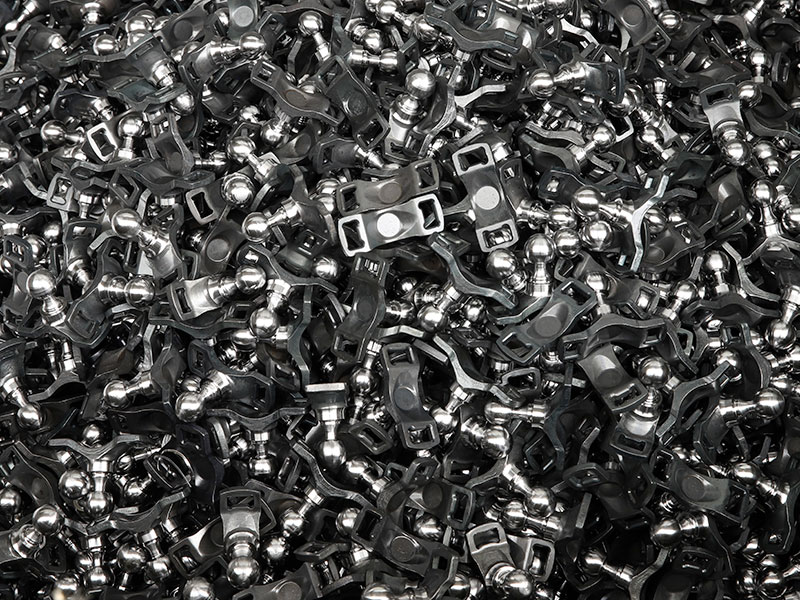
Saving raw materials
With cold forging, up to 70% of material (steel, aluminum, copper) is saved compared to machining process, also reducing the carbon footprint of the product.
Better mechanical properties
Following the hardening due to cold deformation, the mechanical properties of the material are maximized.
Lower production costs
In addition to saving raw materials, we reduce production costs thanks to high productivity: up to 80 pieces per second.
Minimal subsequent work
The possibility of achieving an almost finished shape of the required piece by deformation minimizes any secondary mechanical processes.
Stable and repeatable cycle
We guarantee a stable, repeatable and convenient production cycle for high production volumes.
Highest quality finish
Thanks to our experience, we guarantee an optimal general quality and surface finish.
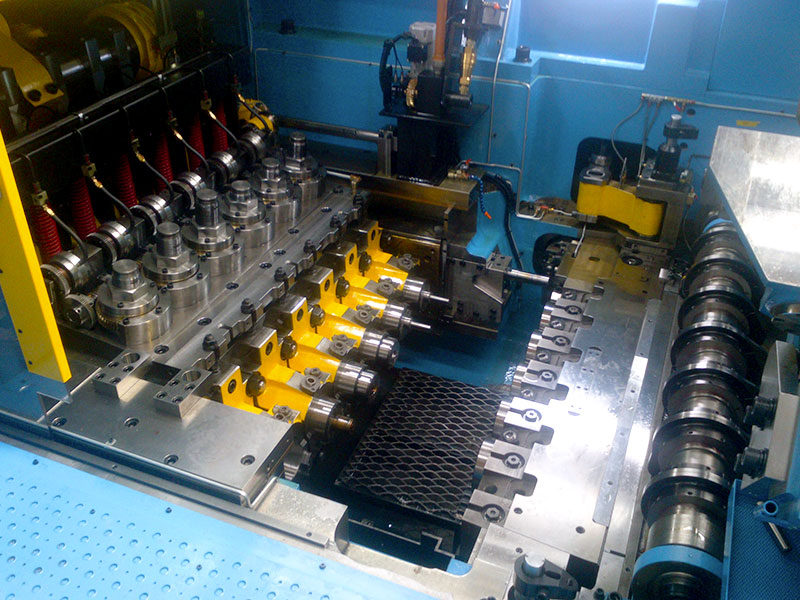
Our machinery
Thanks to our machinery and our technological know-how, we guarantee mass production for high volumes with high quality competitive performance.